Optimizing Manufacturing & Automotive Workflows: The Essential Guide to Workshop Cranes
Introduction
In manufacturing and automotive production, precision, speed, and worker safety are non-negotiable. Workshop cranes play a pivotal role in assembly lines, component handling, and maintenance, helping factories boost productivity, reduce downtime, and minimize workplace injuries.
This guide covers:
✅ Best crane types for automotive & manufacturing
✅ How smart crane tech enhances efficiency
✅ Key features for heavy-duty industrial use
✅ Safety and ROI considerations
Why Manufacturing Needs Specialized Cranes
Manual lifting in production environments leads to:
✖ Bottlenecks in assembly lines
✖ Increased defect rates from improper handling
✖ Worker fatigue and injury risks
✖ Costly equipment damage
The right industrial crane system solves these challenges by:
✔ Enabling precise positioning (±1mm accuracy for sensitive components)
✔ Accelerating cycle times (3-5x faster than forklifts for in-plant moves)
✔ Reducing labor strain (eliminating risky manual lifts)
✔ Integrating with automation (seamless robotic cell coordination)
Best Crane Types for Manufacturing & Automotive
1. Bridge Cranes (Overhead Cranes) – The Production Line Backbone
Best for: High-volume assembly plants, stamping facilities
Capacity: 5-100+ tons
Key Benefits:
- Full facility coverage with runway systems
- Precision controls for delicate part placement
- Automation-ready (PLC-controlled movements)
- Custom configurations (explosion-proof, cleanroom variants)
Ideal Applications:
- Engine block transfers
- Press line feeding
- Robotic weld cell servicing
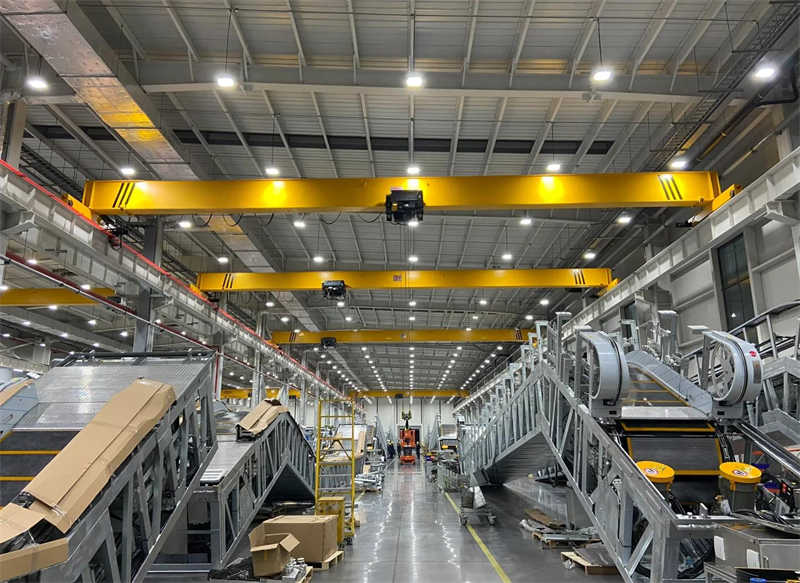
2. Jib Cranes – Flexible Workstation Solutions
Best for: Component staging areas, maintenance bays
Capacity: 0.5-10 tons
Key Benefits:
- 270°-360° rotation for multi-station access
- Modular designs (wall-mounted, freestanding, articulating)
- Fast deployment (install in hours vs. weeks)
Ideal Applications:
- Machined part loading/unloading
- Die changes in press shops
- Electric vehicle battery handling
3. Gantry Cranes – For Heavy Component Movement
Best for: Large part transfers, outdoor storage yards
Capacity: 10-200+ tons
Key Benefits:
- No building modifications required
- Mobile configurations (rail-mounted or rubber-tired)
- Wide spans (up to 30m for frame handling)
Ideal Applications:
- Chassis assembly lines
- Stamping plant scrap removal
- Turbine/transformer handling
4. Smart Hoist Systems – The Automation Edge
Best for: Industry 4.0 smart factories
Features:
- AI-powered load sensing (auto weight detection)
- Vision-guided positioning (camera-assisted alignment)
- Predictive maintenance (IoT vibration monitoring)
ROI Drivers:
- 30% faster changeovers
- 50% reduction in handling damage
- Real-time production data integration
Critical Features for Industrial Cranes
When specifying cranes for manufacturing, prioritize:
🔹 Precision Controls
- Variable frequency drives (VFD) for smooth acceleration
- Micro-speed modes (<1 m/min for delicate placement)
🔹 Durability Enhancements
- Class FEM/ISO duty cycle ratings
- Corrosion-resistant coatings for paint shops
🔹 Safety Systems
- Overload protection (mechanical + electronic)
- Emergency power-down circuits
- Anti-sway technology for long-span lifts
🔹 Future-Proofing
- Modular designs for capacity upgrades
- Open API architecture for MES integration
Case Study: Automotive Tier 1 Supplier Transformation
A major auto parts manufacturer implemented AI-enhanced bridge cranes featuring:
- Automated tool changing
- Digital twin synchronization
- Collision avoidance systems
Results in 12 Months:
✔ 22% increase in press line output
✔ Zero handling-related defects
✔ ROI achieved in 14 months
Selection Guide: Matching Cranes to Applications
Application | Recommended Crane | Why It Works |
---|---|---|
Body-in-white assembly | Automated bridge crane | Precise panel positioning |
Powertrain machining | Articulating jib crane | Multi-machine servicing |
Stamping plant | 50-ton gantry crane | Die set handling |
Battery production | Cleanroom hoist system | Contamination control |
Key Purchasing Considerations
- Cycle Time Requirements → VFD controls reduce move times by 40%
- Floor Space Constraints → Rotary jib cranes maximize tight areas
- Future Expansion Plans → Modular runway systems allow easy extension
- Regulatory Compliance → CMAA Class D/F for heavy industrial use
The Smart Choice for Modern Factories
- High-Mix Production: Smart cranes with quick-change tooling
- Heavy Industry: Robust gantry systems with ≥25% safety margin
- EV Transition: Specialized battery handling solutions
Ready to Upgrade Your Material Handling?
➡ Our industrial crane experts can design a custom solution for your production needs.