Safety Requirements for Lifting Operations and Lifting Machinery
Lifting operations and lifting machinery are integral to modern industrial and construction activities. They significantly enhance productivity and enable the handling of heavy materials with precision. However, the complexity and risks associated with lifting operations demand strict adherence to safety requirements. This guide explores the safety protocols for lifting operations and lifting machinery, focusing on gantry lifts, overhead crane lifts, and other critical equipment. By understanding these safety measures, industries can minimize risks, protect personnel, and ensure operational efficiency.
1. Introduction to Lifting Operations and Lifting Machinery
Lifting operations and lifting machinery are fundamental to modern industrial and construction activities, playing a pivotal role in enhancing productivity and enabling the efficient handling of heavy materials. These operations involve the use of specialized equipment to move, lift, and transport loads vertically or horizontally, making them indispensable in sectors such as manufacturing, logistics, energy, and construction. From bridge cranes in warehouses to gantry cranes in shipyards, lifting machinery is designed to handle a wide range of tasks, from loading and unloading goods to assembling large structures.
However, the complexity and high-risk nature of lifting operations necessitate stringent safety measures. Improper handling, equipment failure, or inadequate training can lead to severe accidents, posing significant threats to personnel safety and operational efficiency. As industries in Singapore and beyond continue to grow, the demand for advanced lifting machinery and safer operational practices has never been greater. This article provides a comprehensive overview of lifting operations and lifting machinery, focusing on their types, applications, and the critical safety protocols required to ensure safe and efficient operations. By understanding the fundamentals of lifting machinery and adhering to industry standards, businesses can minimize risks, protect workers, and optimize productivity in their operations.
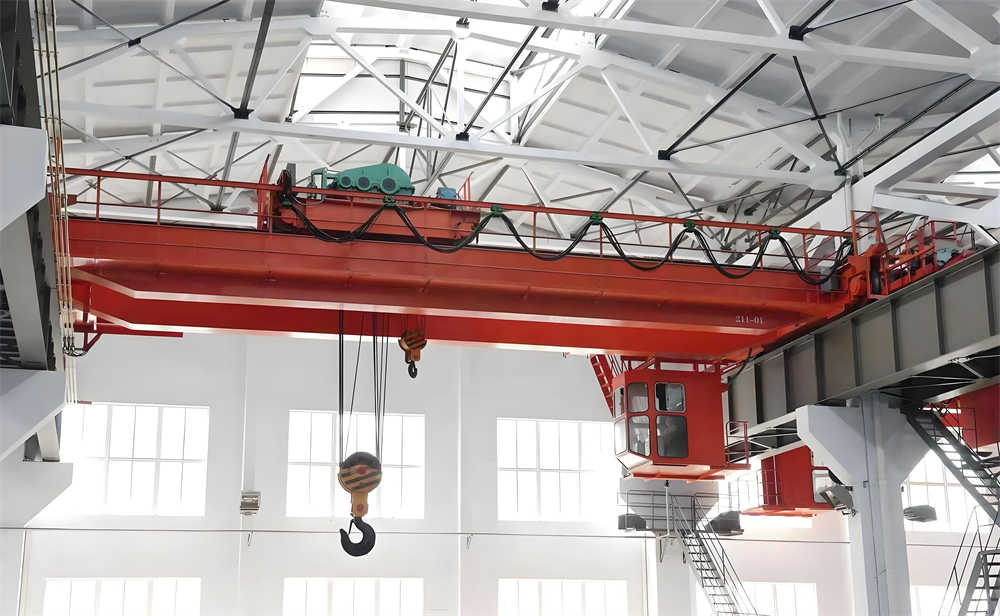
Types of Lifting Machinery
- Gantry Lifts: Used for heavy lifting in ports, shipyards, and large construction sites.
- Overhead Crane Lifts: Ideal for indoor operations in warehouses and manufacturing facilities.
- Tower Cranes: Commonly used in high-rise construction projects.
- Mobile Cranes: Versatile equipment for outdoor lifting tasks.
Each type of lifting machinery has unique safety requirements, which must be followed to prevent accidents and ensure smooth operations.
2. Safety Requirements for Lifting Operations
Lifting operations are integral to industries such as construction, manufacturing, and logistics, enabling the movement of heavy materials with precision and efficiency. However, these operations involve significant risks, including equipment failure, load instability, and human error, which can lead to severe accidents, injuries, or even fatalities. To mitigate these risks, strict adherence to safety requirements is essential.
Safety in lifting operations begins with a thorough risk assessment, evaluating factors such as load capacity, equipment condition, and environmental constraints. Proper operator training and certification are critical, ensuring that personnel are equipped with the knowledge and skills to handle machinery safely. Additionally, the use of personal protective equipment (PPE), clear communication protocols, and regular equipment inspections are fundamental to maintaining a safe work environment.
Modern lifting machinery, such as bridge cranes and gantry cranes, is equipped with advanced safety features like overload limiters, anti-collision systems, and emergency stop buttons. These devices play a crucial role in preventing accidents and ensuring operational safety. Furthermore, compliance with international standards, such as ISO guidelines, and local regulations, like Singapore’s Workplace Safety and Health Act, is mandatory to uphold safety standards.
By prioritizing safety requirements, industries can not only protect their workforce but also enhance productivity and operational efficiency. A proactive approach to safety in lifting operations ensures smooth workflows, minimizes downtime, and fosters a culture of safety in the workplace.
Risk Assessment and Planning
Before commencing any lifting operation, a thorough risk assessment is essential. Key factors to consider include:
- Load Capacity: Ensure the lifting machinery can handle the weight of the materials.
- Work Environment: Check for obstacles, space limitations, and ground conditions.
- Material Characteristics: Assess the size, shape, and stability of the load.
A detailed lifting plan should be prepared, outlining the steps, equipment, and personnel involved.
Operator Qualifications and Training
Lifting operators must possess the necessary skills and certifications. Key requirements include:
- Valid operating licenses.
- Familiarity with the machinery’s controls and safety features.
- Knowledge of emergency response procedures.
Regular training sessions should be conducted to keep operators updated on safety protocols and new technologies.
Safety Measures During Lifting Operations
- Use of Personal Protective Equipment (PPE): Operators and workers must wear helmets, gloves, safety shoes, and harnesses.
- Clear Communication: Establish clear signals and communication channels between operators and ground personnel.
- Avoid Overloading: Never exceed the machinery’s load capacity.
- Monitor Weather Conditions: Avoid lifting operations during strong winds, rain, or other adverse weather conditions.
3. Safety Requirements for Lifting Machinery
3.1 Regular Inspection and Maintenance
Lifting machinery must undergo routine inspections to ensure optimal performance. Key inspection areas include:
- Structural Integrity: Check for cracks, corrosion, or deformities in the machinery’s framework.
- Mechanical Components: Inspect wires, ropes, hooks, and brakes for wear and tear.
- Electrical Systems: Ensure all wiring, switches, and controls are functioning correctly.
A maintenance schedule should be established, with records kept for each inspection and repair.
3.2 Safety Devices and Features
Modern lifting machinery is equipped with advanced safety devices to prevent accidents. These include:
- Overload Limiters: Automatically stop operations if the load exceeds the machinery’s capacity.
- Limit Switches: Prevent the machinery from moving beyond its designated range.
- Anti-Collision Systems: Detect obstacles and halt operations to avoid collisions.
- Emergency Stop Buttons: Allow operators to quickly stop the machinery in case of an emergency.
3.3 Proper Installation and Setup
- Foundation and Support: Ensure the machinery is installed on a stable and level surface.
- Alignment and Calibration: Properly align tracks, rails, and other components to prevent malfunctions.
- Testing: Conduct load tests and trial runs before putting the machinery into operation.
4. Specific Safety Requirements for Gantry Lifts and Overhead Crane Lifts
4.1 Gantry Lifts
Gantry lifts are commonly used in outdoor settings for heavy lifting. Key safety requirements include:
- Stability: Ensure the gantry structure is securely anchored to the ground.
- Load Distribution: Distribute the load evenly to prevent tipping.
- Weather Resistance: Use weather-resistant materials and components to withstand outdoor conditions.
4.2 Overhead Crane Lifts
Overhead crane lifts are widely used in indoor environments. Safety measures include:
- Clear Pathways: Ensure the crane’s path is free from obstacles.
- Regular Lubrication: Keep the crane’s moving parts well-lubricated to prevent friction and wear.
- Operator Visibility: Provide adequate lighting and clear lines of sight for the operator.
5. Emergency Response and Accident Prevention
In the high-risk environment of lifting operations, emergency response and accident prevention are critical components of workplace safety. Despite stringent safety measures, unforeseen incidents such as equipment malfunctions, load drops, or operator errors can occur, posing significant risks to personnel and operations. A well-defined emergency response plan ensures that such situations are handled swiftly and effectively, minimizing harm and downtime.
Key elements of an effective emergency response plan include clear communication protocols, evacuation procedures, and immediate power cutoff mechanisms. Operators and workers must be trained to recognize potential hazards and respond appropriately, whether it involves activating emergency stop buttons, evacuating the area, or administering first aid. Regular emergency drills and simulations help reinforce these protocols, ensuring that all personnel are prepared to act decisively in crisis situations.
Accident prevention, on the other hand, focuses on proactive measures to eliminate risks before they escalate. This includes regular equipment inspections, maintenance schedules, and the use of advanced safety devices such as overload limiters and anti-collision systems. Operator training and safety audits also play a vital role in identifying and addressing potential hazards. By fostering a culture of safety and vigilance, organizations can significantly reduce the likelihood of accidents.
Together, emergency response and accident prevention form the backbone of a comprehensive safety strategy. By prioritizing these aspects, industries can protect their workforce, ensure operational continuity, and comply with safety regulations, ultimately creating a safer and more productive work environment.
Emergency Procedures
- Power Cutoff: Immediately shut off the machinery in case of an emergency.
- Evacuation: Safely evacuate personnel from the affected area.
- Reporting: Notify supervisors and safety personnel about the incident.
Accident Prevention Strategies
- Training Programs: Conduct regular safety training for all personnel.
- Safety Audits: Perform periodic audits to identify and address potential hazards.
- Incident Analysis: Investigate accidents to determine their causes and implement corrective measures.
6. Compliance with Industry Standards and Regulations
Compliance with industry standards and regulations is a cornerstone of safe and efficient lifting operations. These guidelines are designed to ensure that lifting machinery, such as bridge cranes and gantry cranes, is operated, maintained, and inspected in a manner that minimizes risks and protects personnel. Adhering to these standards not only enhances workplace safety but also helps organizations avoid legal penalties and operational disruptions.
Internationally recognized standards, such as those set by the International Organization for Standardization (ISO), provide comprehensive frameworks for the design, operation, and maintenance of lifting equipment. These include guidelines for load testing, safety device functionality, and operator training. Similarly, local regulations, such as Singapore’s Workplace Safety and Health Act and the Code of Practice for Lifting Operations, outline specific requirements tailored to regional safety needs.
Key areas of compliance include regular equipment inspections, certification of operators, and the implementation of safety protocols such as load limits and emergency stop systems. Organizations must also maintain detailed records of inspections, maintenance, and training to demonstrate adherence to regulatory requirements.
By prioritizing compliance with industry standards and regulations, businesses can ensure the safe operation of lifting machinery, protect their workforce, and maintain operational efficiency. This commitment to safety not only fosters a culture of accountability but also enhances the organization’s reputation and reliability in the industry.
International Standards
- ISO Standards: Provide guidelines for the design, operation, and maintenance of lifting machinery.
- OSHA Regulations: Outline safety requirements for lifting operations in the workplace.
Local Regulations
- Workplace Safety and Health Act: Mandates safety protocols for lifting operations and machinery.
- Code of Practice for Lifting Operations: Provides detailed guidelines for safe lifting practices.
7. Conclusion
Safety is paramount in lifting operations and the use of lifting machinery. By adhering to the safety requirements outlined in this guide, industries can minimize risks, protect workers, and enhance operational efficiency. Whether using gantry lifts, overhead crane lifts, or other types of lifting equipment, a proactive approach to safety ensures smooth and successful operations.
Keywords
- Lifting Operation
- Lifting Machinery
- Gantry Lift
- Overhead Crane Lift
- Safety Requirements for Lifting Operations
- Lifting Machinery Safety