Optimizing Material Handling in Small Furniture Factories: How Small Workshop Cranes Boost Efficiency
1. Introduction
The furniture manufacturing industry faces unique challenges when it comes to material handling. Small and medium-sized furniture factories, in particular, often struggle with:
- Heavy raw materials (wood panels, metal fittings) requiring frequent movement
- Bulky semi-finished products that are difficult to maneuver
- Limited floor space that restricts workflow
- High labor costs and safety concerns with manual handling
Traditional manual handling methods are:
- Time-consuming (30-40% of production time spent on material movement)
- Physically demanding (leading to high worker turnover)
- Potentially dangerous (back injuries account for 25% of furniture factory accidents)
Modern small workshop crane solutions can:
✔ Increase material handling efficiency by 50-70%
✔ Reduce workplace accidents by 80%
✔ Improve space utilization by 30-40%
✔ Lower long-term operational costs
This comprehensive guide explores how small furniture manufacturers can transform their material handling processes through strategic crane system implementation.
2. Material Handling Challenges in Furniture Production
2.1 Critical Movement Points
- Raw Material Receiving
- Unloading trucks (especially large wood panels)
- Transporting to storage or cutting stations
- Production Process Flow
- Moving cut pieces to edge banding
- Transferring components to assembly
- Finished product movement to finishing/packing
- Storage and Shipping
- Vertical storage retrieval
- Loading finished products for delivery
2.2 Unique Industry Requirements
Precision Handling Needs:
- Delicate surfaces requiring scratch prevention
- Fragile components (glass, veneers)
Space Constraints:
- Narrow aisles (often < 2m wide)
- Low ceiling heights (typically 3-4m)
- Congested work areas
Ergonomic Considerations:
- Heavy lifting (standard MDF panel = 70-100kg)
- Repetitive motion injuries
3. Optimal Crane Solutions for Furniture Makers
3.1 Jib Cranes – The Space-Saving Workhorse
Best Applications:
- Fixed position material transfer
- Machine servicing/maintenance
- Loading/unloading stations
Dongqi Recommendations:
- DQ-BZ Wall-Mounted Jib
- Capacity: 0.5-2 tons
- Rotation: 180° or 360°
- Ideal for: Panel cutting to edge banding transfer
- DQ-PK Freestanding Jib
- No wall support needed
- 360° rotation coverage
- Perfect for assembly area flexibility
Case Example: A cabinet manufacturer installed three DQ-BZ cranes between cutting and edge banding stations, reducing transfer time from 15 to 4 minutes per panel.
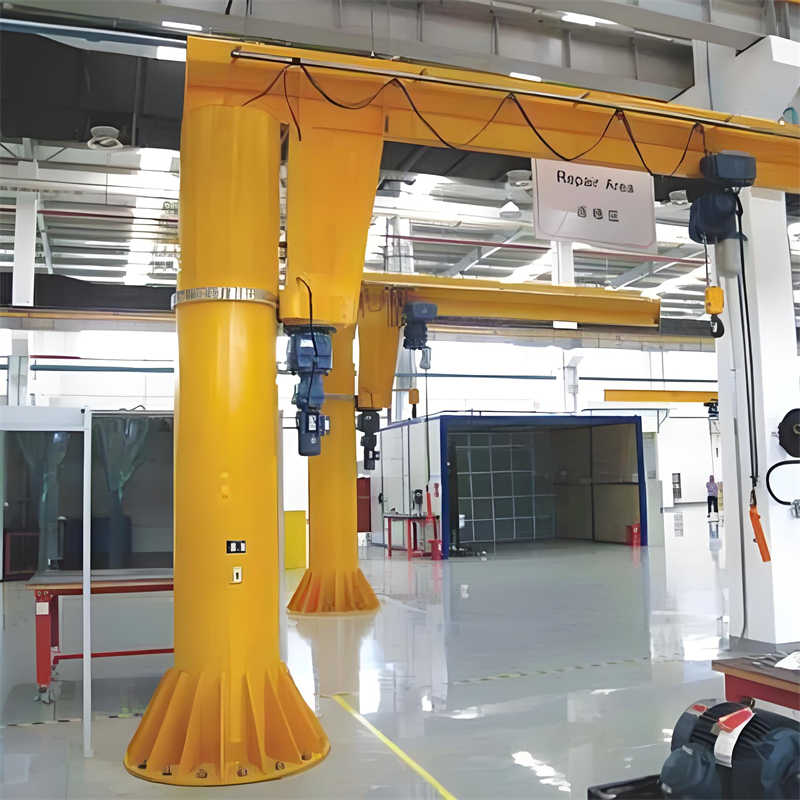
3.2 Light Gantry Cranes – Flexible Floor Coverage
Key Advantages:
- Mobile across work areas
- No permanent installation
- Modular expansion possible
Typical Configurations:
- Aluminum frame (lightweight)
- Electric hoist with variable speed
- Anti-sway technology
Implementation Tip: Use for moving finished cabinet carcasses from assembly to finishing area.
3.3 Intelligent Rail Systems – Automated Flow
Advanced Solution Features:
- I-beam track ceiling mounting
- Programmable electric hoists
- ERP system integration
Operational Benefits:
- Just-in-time component delivery
- Reduced WIP inventory
- Traceable material flow
Real Results: One custom furniture producer achieved 35% reduction in work-in-process after implementing rail system.
4. Space Optimization Strategies for Furniture Factories
Effective space utilization is critical for small furniture manufacturers facing floor space constraints. This section provides detailed, actionable strategies to maximize your workshop’s potential through intelligent crane system implementation.
4.1 Vertical Space Utilization Techniques
A. Overhead Crane Configurations
- Low-Headroom Single Girder Systems
- Minimum clearance: Just 150mm below ceiling
- Ideal for: Workshops with 3-4m ceiling heights
- Configuration example:
- 5m span crane with 1-ton capacity
- End trucks mounted directly to building columns
- Wireless pendant control for floor-level operation
- Mezzanine Integration Solutions
- Dual-level material flow:
- Ground floor: Primary processing
- Mezzanine: Component storage
- Crane specifications:
- 500kg capacity jib crane for vertical transfers
- 2m outreach to cover both levels
- Safety interlocks for mezzanine edge protection
- Vertical Carousel Storage Systems
- Combined with light cranes for:
- Small part retrieval (hardware, fittings)
- Finished component staging
- Typical specs:
- 8-10 storage levels
- Integrated vacuum lifters
- 90-second retrieval time
B. Ceiling-Mounted Systems
- Monorail Networks
- Layout options:
- Straight-line for linear processes
- Oval circuits for continuous flow
- Capacity range: 250kg-2 tons
- Turnkey package includes:
- Track system
- Electric hoist
- Switching junctions
- Workstation Bridge Cranes
- Micro-environments for:
- Sanding stations
- Finishing areas
- Quality control points
- Compact dimensions:
- 3m span × 2m length
- 200kg capacity
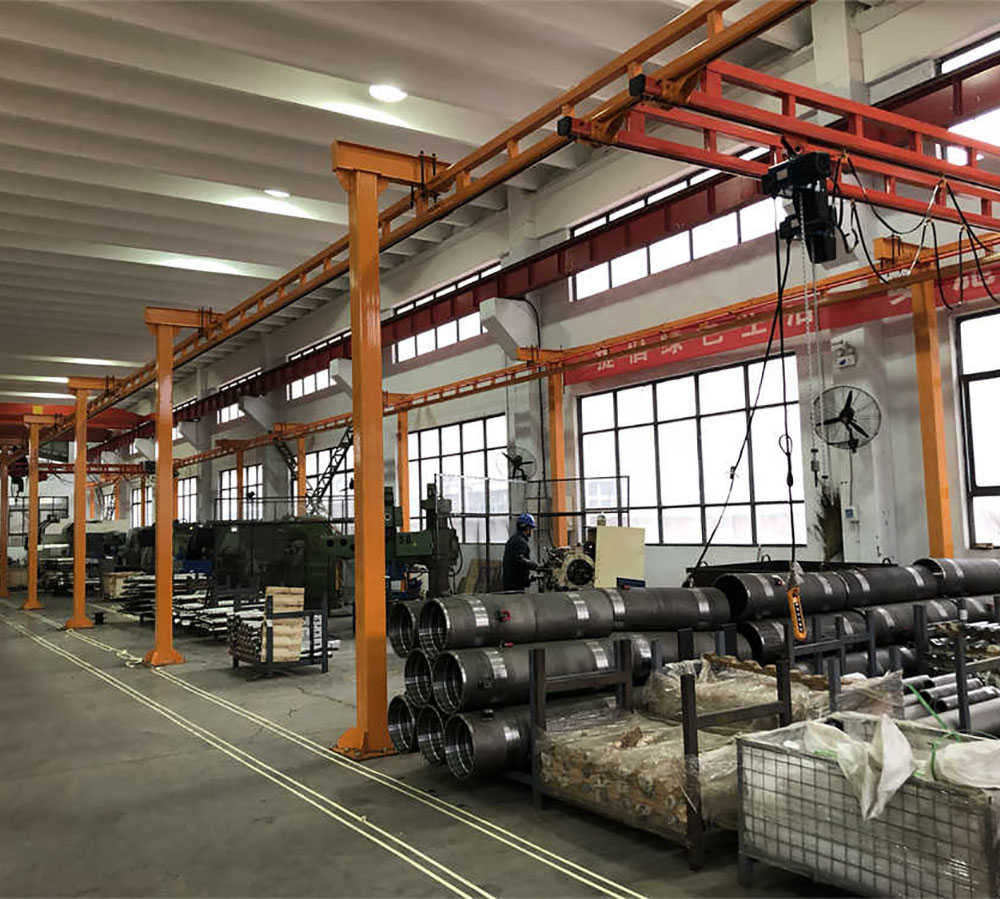
4.2 Horizontal Space Optimization
A. Workcell Design Principles
- U-Shaped Production Lines
- Crane placement strategy:
- Central jib crane covers all stations
- 2.5m radius provides full coverage
- Material flow:
- One-way component movement
- Zero cross-traffic
- Nested Workstation Layouts
- Space-saving approach:
- 1.2m minimum aisle width
- Overlapping crane coverage zones
- Equipment specs:
- 1-ton capacity jib cranes
- 210° rotation range
B. Mobile Equipment Solutions
- Track-Mounted Gantry Systems
- Installation options:
- Floor-embedded rails
- Surface-mounted tracks
- Operational benefits:
- 6m span covers two parallel lines
- 5m/min travel speed
- Modular Work Platforms
- Combined with lifting equipment:
- Scissor lifts with crane attachments
- Height-adjustable workbenches
- Typical configuration:
- 1.5m × 3m platform
- 500kg dual-purpose capacity
4.3 Hybrid Storage Solutions
A. Dynamic Racking Systems
- Movable Aisle Storage
- Crane integration:
- Narrow-aisle jib cranes
- 90° rotating hoists
- Density improvement:
- 40% more storage capacity
- 1m minimum aisle width
- Cantilever Rack Cranes
- Specialized for:
- Long material storage (mouldings, trims)
- Panel retrieval
- Technical specs:
- 3m cantilever arms
- Vacuum plate lifter
B. Automated Storage/Retrieval
- Mini-Load AS/RS
- Small footprint version:
- 3m height × 2m footprint
- 50 storage bins
- Crane interface:
- Automatic hand-off stations
- Barcode tracking
- Vertical Lift Modules
- Space savings:
- 60% less floor space than shelving
- Crane loading:
- Integrated lift platforms
- 150kg capacity per insertion
4.4 Specialized Furniture Handling Solutions
A. Panel Handling Systems
- Vacuum Lifters
- Configuration options:
- Single-point for small panels
- Multi-point for large sheets
- Performance specs:
- 3-second pickup/release
- 90° panel rotation
- Edge-Gripping Cranes
- For delicate materials:
- Veneered panels
- Lacquered surfaces
- Technical features:
- Pressure-sensitive grips
- Automatic centering
B. Assembly Assist Systems
- Balancing Cranes
- Ergonomic benefits:
- Zero-gravity feel
- 10:1 weight reduction
- Typical use:
- Cabinet assembly
- Door hanging
- Positioning Arms
- Precision handling:
- 0.5mm repeatability
- 6-axis control
- Applications:
- Detailed joinery
- Hardware installation
Implementation Checklist
- Pre-Installation Audit
- Ceiling load capacity verification
- Electrical supply assessment
- Workflow analysis
- Space Mapping
- 3D laser scanning
- Traffic flow simulation
- Safety zone marking
- Performance Metrics
- Pre-installation baseline
- Post-installation targets:
- Space utilization %
- Handling time reduction
- Damage rate improvement
This comprehensive space optimization approach enables furniture manufacturers to achieve 30-50% better space utilization while improving material handling efficiency and worker safety. Each solution can be customized based on specific workshop dimensions, production volumes, and product characteristics.
5. Implementation Roadmap
Phase 1: Assessment (1 Week)
- Value stream mapping
- Bottleneck identification
- Load analysis (weights, frequencies)
Phase 2: Design (2 Weeks)
- 3D layout simulation
- Interference checking
- Operator training planning
Phase 3: Pilot (1 Month)
- Start with highest-impact area
- Measure KPIs:
- Handling time reduction
- Damage rate decrease
- Space savings
6. Cost-Benefit Analysis
Comparative Data:
Metric | Manual Handling | Crane System |
---|---|---|
Daily Capacity | 8 tons | 20 tons |
Required Staff | 4 workers | 1 operator |
3-Year Cost | $42,000 | $22,500 |
Damage Rate | 3-5% | <0.5% |
ROI Calculation:
- Average investment: $15,000-$35,000
- Payback period: 9-14 months
- Lifetime savings: 3-5x investment
7. Success Story: Zhejiang Cabinet Maker
Initial Challenges:
- 300 units/month capacity stuck
- 15-day production lead time
- High worker turnover
Solution Implemented:
- 3 x DQ-PK jib cranes
- 1 x 2-ton gantry system
- Vacuum lift attachments
Measured Outcomes:
- 40% faster order fulfillment
- 62% lower handling costs
- 0 lifting-related injuries in 18 months
8. Frequently Asked Questions
Q: Our building is old – can it support cranes?
A: Dongqi provides structural assessment and reinforcement solutions.
Q: How disruptive is installation?
A: Most systems installed in 1-2 days without production stoppage.
Q: What about dust collection interference?
A: We design around existing ductwork and utilities.