Metallurgical Crane Retrofit Construction Program for Pakistani Customers
Metallurgical Crane Retrofit Construction Program for Pakistani Customers
Introduction
Metallurgical cranes are critical equipment in industrial production, and their performance and safety directly impact production efficiency and operational safety. With the continuous advancement of technology and evolving production demands, retrofitting and upgrading existing metallurgical cranes have become increasingly important. This construction program aims to enhance the crane’s load-bearing capacity, operational stability, and intelligence level through systematic renovation measures, ensuring compliance with the high standards required by modern production. The retrofit process will cover various aspects, including pre-construction preparation, construction steps, quality control, safety measures, and maintenance, to ensure the project is executed smoothly and achieves the desired results.
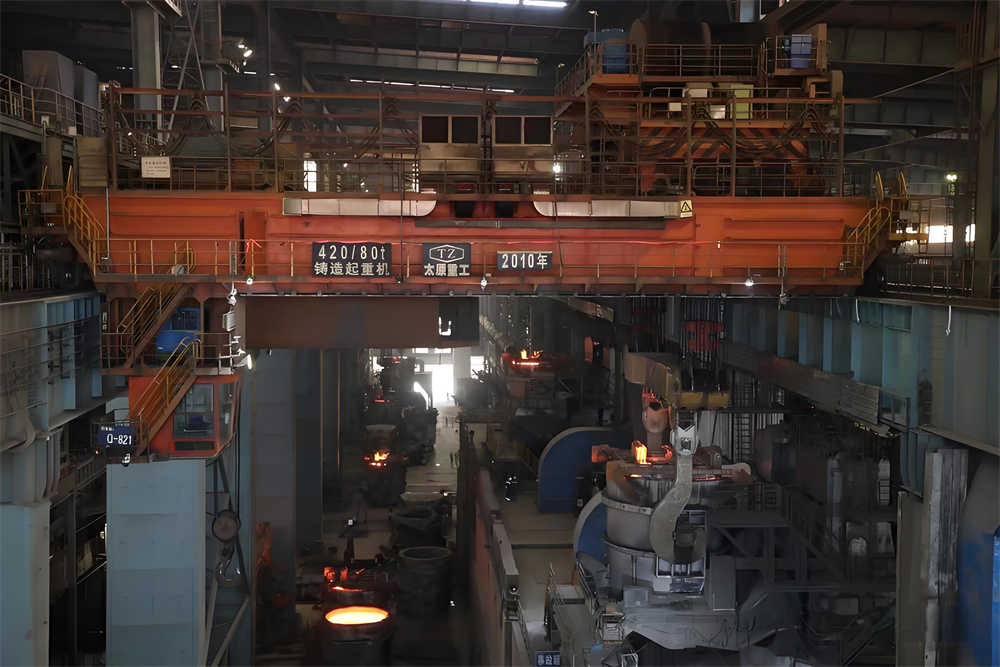
Intelligent Upgrade and Retrofit of Metallurgical Casting Cranes
Program Overview and Objectives
Metallurgical cranes are essential equipment in industries such as steel smelting and heavy material handling. Their performance and safety directly influence production efficiency and personnel safety. Therefore, conducting a comprehensive assessment and upgrade of metallurgical cranes is crucial. The purpose of this retrofit program is to evaluate and enhance existing cranes to improve their load-bearing capacity, handling precision, and operational stability while strengthening safety performance. This ensures the equipment remains efficient and reliable during long-term operation.
The primary goals of this retrofit program are:
- Enhanced Efficiency: Enable cranes to operate efficiently in complex environments.
- Reduced Failure Rates: Minimize equipment downtime and maintenance costs.
- Extended Service Life: Improve the durability and longevity of the cranes.
- Safety Assurance: Ensure compliance with national safety standards and provide a safe working environment.
Through this retrofit, the reliability and safety of the cranes will be significantly improved, reducing maintenance costs and increasing production efficiency. The program will comprehensively evaluate and upgrade the crane’s structure, electrical systems, hydraulic systems, and lubrication systems to meet both national standards and the specific requirements of Pakistani industries.
Pre-Construction Preparation and Evaluation
Existing Equipment Condition Assessment
Before commencing the retrofit, a thorough assessment of the current condition of the metallurgical cranes is essential. This evaluation aims to accurately identify the operational status of the equipment, providing a scientific basis for the retrofit design and construction plan. The assessment covers the following key areas:
- Main Structure Inspection:
- Conduct a detailed inspection of the crane’s metal structure, including the main girder, end girder, and running rails.
- Use non-destructive testing techniques such as ultrasonic and magnetic particle testing to identify issues like fatigue deformation, cracks, weld defects, or corrosion.
- Transmission System Evaluation:
- Inspect critical components such as motors, reducers, couplings, and brakes.
- Check for excessive wear, lubrication issues, and fastener looseness to ensure stable and reliable operation under high-intensity workloads.
- Electrical Control System Analysis:
- Evaluate the condition of the electrical control system, including control cabinets, frequency converters, sensors, and contactors.
- Identify aging, damage, or performance degradation to ensure the system’s automation and safety functions operate correctly.
- Safety Device Verification:
- Test safety devices such as overload protection, limit switches, emergency stop buttons, and anti-collision systems.
- Ensure these devices function effectively to prevent accidents during operation.
This comprehensive assessment provides critical data for the retrofit design, ensuring the upgraded cranes meet production requirements and operate safely and efficiently.

Construction Team Formation and Training
A skilled and experienced construction team is essential for the successful execution of the retrofit project. The team should include professionals such as mechanical engineers, electrical engineers, safety supervisors, and project managers. Each member must have extensive experience in metallurgical crane retrofits and a thorough understanding of the project requirements.
Before construction begins, all team members must undergo rigorous training, covering:
- Implementation steps of the retrofit program.
- Detailed operational procedures.
- Safety protocols and emergency response measures.
This training ensures that team members can execute their tasks accurately and safely, minimizing risks and ensuring high-quality workmanship.
Pre-Construction Key Tasks and Responsibilities
Task | Responsible Person | Key Points |
---|---|---|
Condition Assessment | Mechanical/Electrical Engineers | Inspect main structure, transmission system, electrical systems, and safety devices. |
Team Formation | Project Manager | Assemble a team with expertise in mechanical, electrical, and safety fields. |
Team Training | Safety Supervisor | Train on retrofit steps, safety norms, and emergency measures. |
Material Procurement | Project Manager/Purchasing Specialist | Procure high-strength steel, wear-resistant bearings, and advanced electrical components. |
Tool Preparation | Tool Manager | Prepare and inspect tools such as cranes, welding machines, and electric wrenches. |

Construction Materials and Tools Preparation
All necessary materials, including high-strength steel, wear-resistant bearings, and advanced electrical components, must be procured in advance. Tools and equipment such as cranes, welding machines, and electric wrenches should be inspected and maintained to ensure they are in optimal condition for the retrofit.
Retrofit Construction Steps and Processes
Dismantling and Cleaning
Before starting the retrofit, ensure all safety measures are in place. Disconnect the power supply and electrical connections to prevent accidents. Dismantle the crane step-by-step according to a pre-planned sequence, ensuring the surrounding environment is protected from debris and contamination.
After dismantling, thoroughly clean all components to remove oil, rust, and impurities. This prepares the parts for replacement, upgrading, and reassembly.
Replacement and Upgrading of Key Components
Replace severely worn or degraded components identified during the assessment. This includes drive shafts, gearboxes, brakes, and other critical parts. Strengthen the crane’s main structure as needed through welding, grinding, or replacing structural components.
Upgrade the electrical control system with advanced technologies such as variable frequency drives (VFDs) and programmable logic controllers (PLCs) to achieve precise control and higher operational efficiency.
Control System Modification and Optimization
Upgrade the crane’s electrical control system with advanced algorithms and sensor technology to enable intelligent control and management. Optimize control logic to improve response speed and stability, reducing operational errors and enhancing efficiency.
Implement remote monitoring and fault diagnosis systems to allow real-time access to operational data and status information. This enables quick identification and resolution of potential issues, reducing maintenance costs and improving equipment reliability.
Safety Device Installation and Testing
Install and test safety devices such as fall prevention systems, limit switches, and overload protection devices in compliance with the latest safety standards. Conduct rigorous testing to ensure these devices function effectively during emergencies.
Construction Quality Control and Safety
Quality Control Standards and Measures
Implement high-standard quality control measures throughout the retrofit process. This includes material inspection, construction process monitoring, and acceptance testing. Maintain detailed records of all construction activities for future reference and traceability.
Safety Management System and Protocols
Establish a comprehensive safety management system to ensure the safety of all personnel and equipment. Conduct regular safety inspections and provide ongoing training to construction teams. Use advanced monitoring technologies to track the construction process in real time, ensuring compliance with safety norms.
Post-Retrofit Acceptance and Maintenance
Acceptance Criteria and Procedures
After completing the retrofit, conduct rigorous testing to verify the crane’s load-bearing capacity, handling precision, and safety device functionality. Engage a qualified third-party testing organization to independently evaluate the crane’s performance and ensure compliance with national standards.
Maintenance and Upkeep Plan
Develop a detailed maintenance plan to ensure the crane’s long-term performance and safety. This includes regular lubrication, fastener inspection, and cleaning. Maintain a comprehensive equipment maintenance record to track repair history and identify potential issues early.
Conclusion
This metallurgical crane retrofit construction program is designed to meet the high standards required by modern industrial production. By enhancing the crane’s load-bearing capacity, operational stability, and safety performance, this program ensures reliable and efficient operation in demanding environments. For Pakistani customers, this retrofit offers a cost-effective solution to improve production efficiency, reduce maintenance costs, and ensure compliance with safety standards. Through meticulous planning, execution, and maintenance, this program provides a solid foundation for long-term operational success.