Ensuring Safety in Bridge Crane Lifting Operations
Bridge cranes are indispensable heavy equipment in the industrial field, and their safe operation is critical to maintaining production efficiency and ensuring personnel safety. In complex operating environments, ensuring foolproof lifting operations requires meticulous planning, thorough inspections, and strict adherence to safety protocols. This article provides a detailed guide on safety precautions for bridge crane lifting operations, covering pre-operation preparations, equipment inspections, environmental assessments, operator training, and emergency response measures.
1. Safety Preparation Before Operation
1.1 Review of the Operation Plan
Before initiating any lifting operation, a comprehensive review of the operation plan is essential. This includes:
- Assessing the feasibility and safety of the lifting task.
- Ensuring that all parameters, such as the crane’s rated lifting capacity, span, and lifting height, are within the design limits.
- Avoiding overload operations or improper usage that could lead to mechanical failures or accidents.
1.2 Safety Environment Improvement
The operation site must be prepared to ensure a safe working environment:
- Remove all obstacles, such as scattered objects, sharp materials, or temporary stacks, that could interfere with the crane’s operation.
- Ensure the crane’s operational path is clear of personnel and equipment to prevent collisions or accidents.
- Set up clear and visible safety warning signs and isolation facilities to demarcate the lifting area.
1.3 Establishment of Command and Coordination Mechanisms
A well-defined command and coordination system is crucial for safe lifting operations:
- Designate a specialized commander to oversee the operation.
- Establish clear communication protocols and command signals to ensure all personnel understand their roles.
- Develop emergency response plans and liaison mechanisms to handle unexpected situations effectively.
2. Crane Equipment Safety Inspection
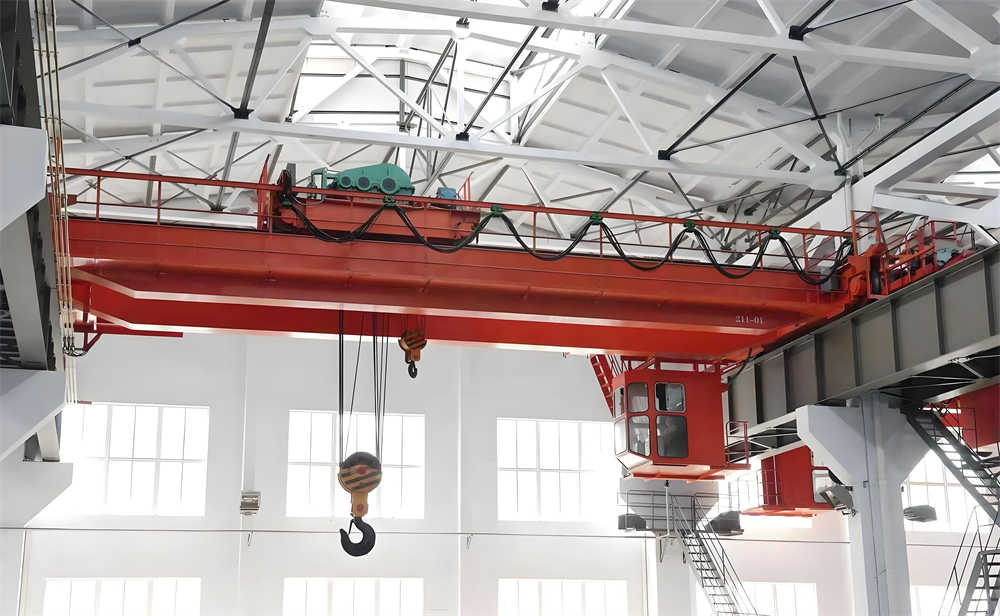
2.1 Inspection of Equipment Appearance and Structure
A thorough inspection of the crane’s physical condition is necessary before operation:
- Check the metal structure, including the bridge frame, end beams, and trolley frame, for cracks, slag inclusions, or leaks.
- Inspect bolted joints to ensure they are tightened and secure.
- Examine wear-prone components, such as pulleys, wire ropes, and hooks, for signs of wear, broken wires, or damage.
2.2 Functional Testing
Conduct functional tests to verify the crane’s operational performance:
- Test the lifting mechanism to ensure smooth operation without abnormal noises or vibrations.
- Check the braking system to confirm it can reliably stop and decelerate.
- Verify the trolley and crane movement for smooth operation and proper coordination between components.
- For cranes with variable amplitude functions, test the luffing mechanism to ensure precise control.
2.3 Verification of Safety Devices
Safety devices are critical for preventing accidents during lifting operations:
- Inspect limiters (e.g., travel and lifting limiters) to ensure they function correctly at extreme positions.
- Check buffers to confirm they can absorb impact forces effectively.
- Verify anti-unhooking devices to prevent accidental detachment of the hook.
- Maintain a detailed record of safety device inspections for accountability and future reference.
3. Lifting Operation Environment Assessment
3.1 Division and Identification of the Operation Area
The lifting area must be clearly defined and marked:
- Use safety warning signs and barriers to demarcate the operational zone.
- Highlight key areas, such as lifting points, supporting structures, and critical pathways, to guide operators.
3.2 Assessment of Ground Bearing Capacity
The ground’s ability to support the crane and load is critical:
- Evaluate soil properties, geological conditions, and moisture levels to determine ground stability.
- Reinforce the ground if necessary, using methods such as foundation strengthening or steel plate laying, to ensure adequate bearing capacity.
3.3 Meteorological Conditions and Lighting Requirements
Environmental factors significantly impact lifting safety:
- Monitor weather conditions and suspend operations during adverse conditions, such as strong winds, heavy rain, or thunderstorms.
- Ensure adequate lighting at the worksite to enable clear visibility of the load and surroundings.
- Use weatherproof lighting equipment to maintain illumination during unfavorable conditions.
4. Operator Training and Qualifications
4.1 Operation Skills Training
Operators must undergo comprehensive training to handle cranes safely and efficiently:
- Provide theoretical and practical training on crane operation principles, procedures, and troubleshooting.
- Emphasize the importance of precision and control during lifting operations.
4.2 Safety Knowledge Education
Safety awareness is crucial for preventing accidents:
- Educate operators on safety protocols, hazard identification, and emergency response measures.
- Conduct regular safety drills to reinforce knowledge and preparedness.
4.3 Operation Qualification Review
Ensure operators meet legal and operational standards:
- Assess operators’ skills and knowledge through rigorous testing and evaluation.
- Issue certifications only to qualified individuals who demonstrate competence in crane operations.
5. Safety Operating Procedures for Lifting Operations
5.1 Standardization of the Lifting Operation Process
Follow a standardized process to minimize risks:
- Develop a detailed lifting plan, including load weight, dimensions, lifting points, and operational sequences.
- Designate a supervisor to oversee the operation and ensure compliance with the plan.
5.2 Requirements for the Use of Slings and Rigging
Proper selection and inspection of lifting accessories are essential:
- Inspect slings, hooks, and rigging for wear, cracks, or defects before use.
- Choose appropriate slings and rigging based on the load’s weight, size, and environmental conditions.
- Replace damaged or worn-out accessories immediately to prevent accidents.
5.3 Emergency Response Measures
Prepare for unexpected situations with well-defined emergency protocols:
- Equip the worksite with emergency stop buttons, firefighting equipment, and first-aid kits.
- Train operators on evacuation routes and emergency procedures.
- Conduct regular drills to ensure quick and effective responses during emergencies.
6. Record-Keeping and Documentation
6.1 Safety Device Verification Record
Maintain a detailed log of safety device inspections:
Safety Device | Verification Content | Result | Inspector | Date |
---|---|---|---|---|
Travel Limiter | Stops reliably at limit positions | Pass/Fail | _ | _ |
Lifting Limiter | Stops reliably at limit positions | Pass/Fail | _ | _ |
Buffer | Effective impact absorption | Pass/Fail | _ | _ |
Anti-Unhooking Device | Prevents accidental hook detachment | Pass/Fail | _ | _ |
Other Safety Devices | _ | Pass/Fail | _ | _ |
6.2 Functional Testing Record
Document the results of functional tests:
Test Item | Test Content | Result | Tester | Date |
---|---|---|---|---|
Lifting Function | Smooth operation, no abnormal noises | Pass/Fail | _ | _ |
Brake Performance | Reliable stopping and deceleration | Pass/Fail | _ | _ |
Crane Movement | Smooth operation, no abnormal noises | Pass/Fail | _ | _ |
Trolley Movement | Smooth operation, no abnormal noises | Pass/Fail | _ | _ |
Luffing Function | Precise control of amplitude (if applicable) | Pass/Fail | _ | _ |
Pulley and Wire Rope | Wear and wire breakage within limits | Pass/Fail | _ | _ |
Conclusion
Ensuring the safety of bridge crane lifting operations requires a holistic approach that encompasses thorough preparation, rigorous inspections, environmental assessments, operator training, and adherence to safety protocols. By following the guidelines outlined in this article, businesses can minimize risks, enhance operational efficiency, and safeguard personnel and equipment. A proactive commitment to safety not only prevents accidents but also fosters a culture of responsibility and excellence in industrial operations.