Electric single beam crane and electric hoist installation plan sample
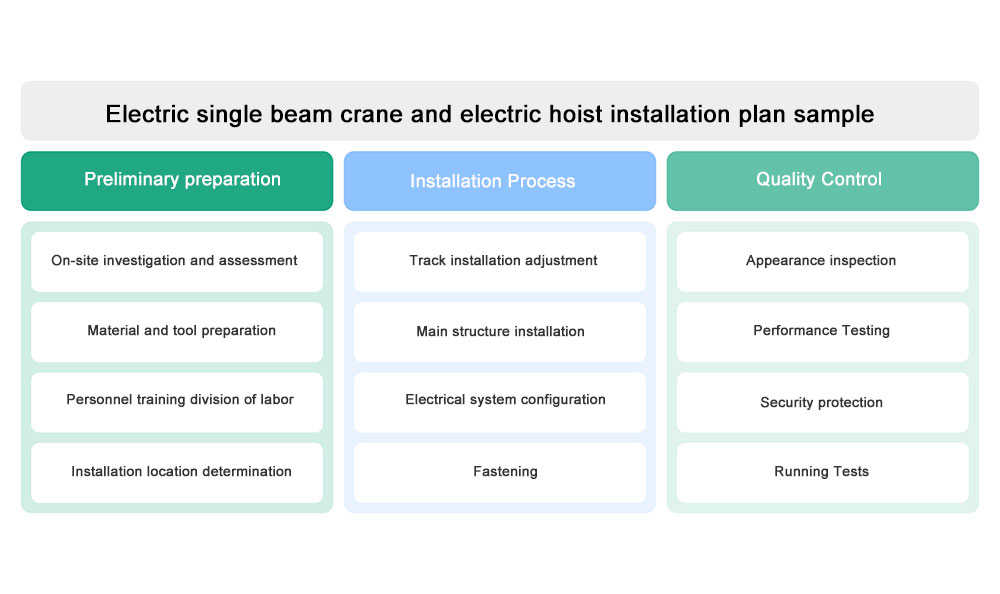
As an indispensable lifting equipment in modern industry, the accuracy and execution efficiency of the installation plan of electric single-beam cranes and electric hoists are directly related to the safety and efficiency of subsequent production operations. This plan sample aims to provide a detailed and systematic installation guide, covering from pre-installation preparation to the refinement of installation steps, and then to the final quality inspection and acceptance. Through scientific planning and rigorous operation, ensure that electric single-beam cranes and electric hoists can stably and efficiently serve various industrial production scenarios. The plan not only focuses on the grasp of technical details, but also emphasizes safety management and quality control during the installation process, and strives to provide users with a comprehensive and reliable installation reference.
Installation plan overview
As an indispensable material handling equipment in the modern industrial production environment, the efficient and stable operation of electric single-beam cranes and electric hoists plays a decisive role in improving production efficiency and ensuring the safety of the working environment. Therefore, the quality of its installation directly affects the subsequent production efficiency and safety. In order to ensure the smooth installation process of electric single-beam cranes and electric hoists, this installation plan is comprehensively planned and designed. This installation plan aims to elaborate the installation process of electric single beam crane and electric hoist, ensuring that each step is accurate and correct, so as to ensure the stable operation of the equipment. The plan covers the whole process from pre-installation preparation to installation quality inspection and acceptance, aiming to provide a detailed instruction manual for the installation team to guide the installation team to complete the installation task efficiently and accurately.
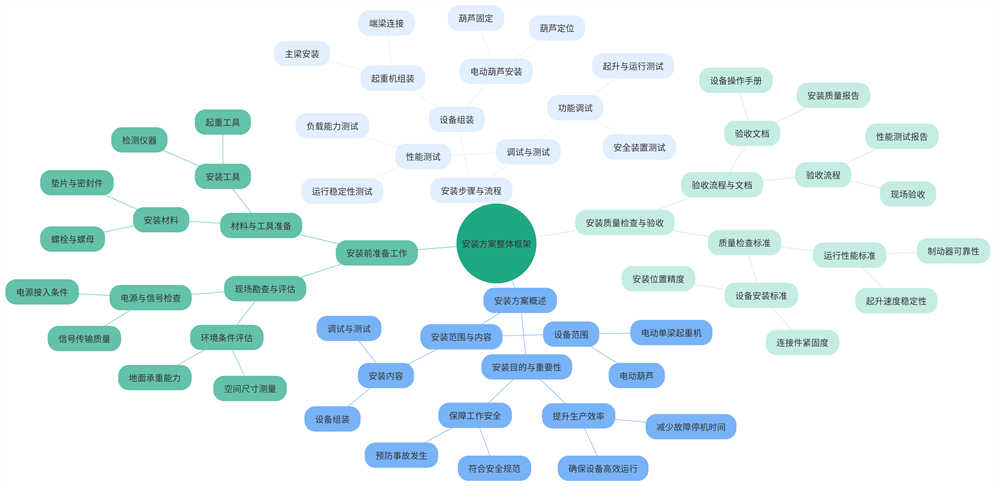
Pre-installation preparations
Installation site survey and assessment
Before officially starting the installation work, a comprehensive and detailed survey and assessment of the installation site is an essential and important step. First of all, it is necessary to conduct an in-depth analysis of the overall structure of the plant, including but not limited to load-bearing capacity, spatial layout, and seismic performance, to ensure the safety and stability of the installation environment. Especially for high-precision equipment or heavy cranes, it is necessary to ensure that the plant structure can withstand the load and vibration generated during the operation of the equipment to avoid safety hazards caused by structural problems.
In addition to a comprehensive inspection of the hardware conditions of the plant itself, it is also necessary to carefully evaluate the safety conditions of the site, such as ground flatness, obstacle clearance, fire protection facilities and other details. Through on-site surveys by professionals, potential safety hazards can be discovered and resolved in advance to ensure that the installation work can be carried out in a safe and orderly environment. In addition, based on the survey results, determine the appropriate installation location and layout plan to ensure the convenience and efficiency of operation after the equipment is put into use.
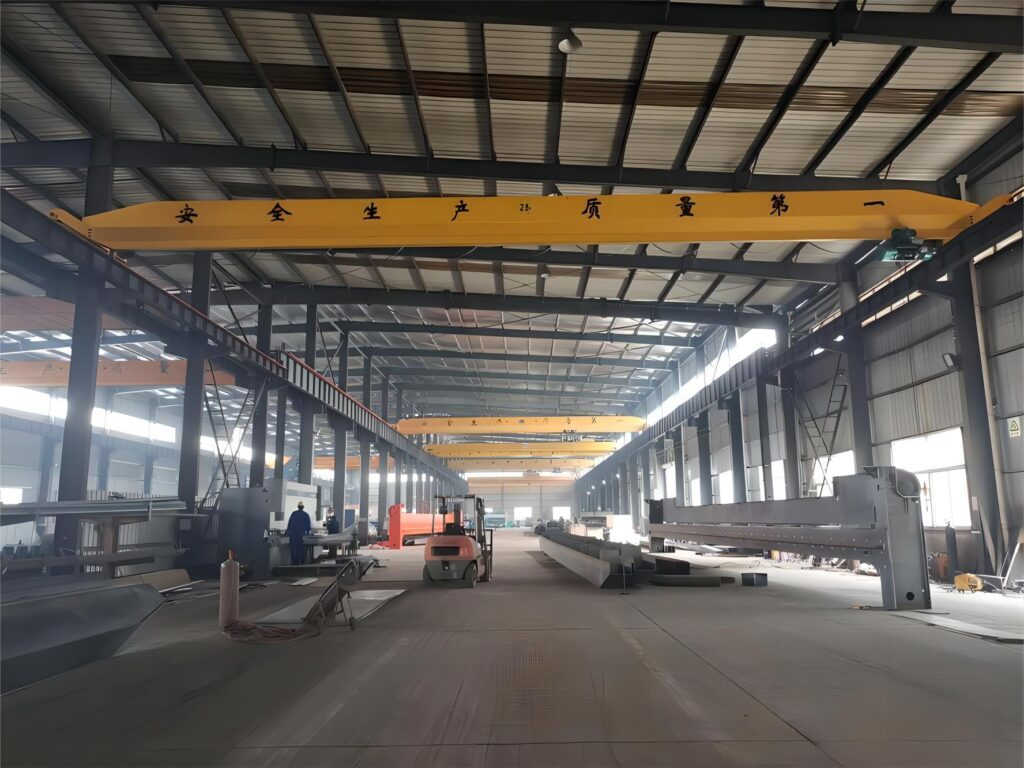
On-site investigation record form
Exploration projects | Survey content | Survey results | Note |
Factory Structure | Weight-carrying capacity | _ | Such as load-bearing capacity assessment report, etc. |
Space layout | _ | Such as layout sketches or photos, etc. | |
Seismic resistance | _ | Such as seismic test report, etc. | |
Safety status | Ground flatness | _ | |
Installation location | Recommended location | _ | |
Other | _ | _ | Such as on-site special environment, potential hidden dangers, etc. |
Installation materials and tool preparation list
Category | Material/Tool Name | Quantities | Note |
Material | Crane tracks | _ | Comply with relevant national standards and design specifications |
Tool | Lifting equipment | _ | Check and test before put into use |
Other | _ | _ | Such as safety equipment, auxiliary tools, etc. |
Preparation of installation materials and tools
According to the design plan and construction plan, all necessary installation materials and tools need to be prepared in advance. In terms of materials, this includes but is not limited to crane rails, main structural parts, electrical components, etc. All materials must comply with relevant national standards and design specifications to ensure reliable quality and stable performance. In terms of tools, prepare lifting equipment, bolt tightening tools, electrical testing instruments, etc. All tools must be inspected and tested before being put into use to ensure that they are in good working condition and avoid installation delays or quality problems caused by tool failure.
Training and division of labor for installation personnel
Before the formal installation begins, systematic and professional training for all personnel involved in the installation work is a crucial management link. The training content should cover the structural principles, operating procedures, safety instructions, and emergency handling procedures of electric single-beam cranes and electric hoists, ensuring that each installer has the necessary knowledge reserves and skill levels and can strictly follow the operating procedures.
At the same time, in order to improve the overall installation efficiency and ensure the orderly progress of the work process, the installation team needs to be carefully divided. According to the professional expertise and work ability of each installer, clarify their specific responsibilities and tasks during the installation process, such as hoisting group, fixing group, electrical connection group, etc. Through reasonable division of labor, everyone’s advantages can be maximized, and inefficiency or even safety accidents caused by poor communication or unclear responsibilities can be effectively avoided.
Electric single-beam crane installation steps
Track installation and adjustment
The installation of the track is the basis for the installation of the electric single-beam crane, and its installation accuracy directly affects the operation stability and safety of the crane. During the installation process, a series of measures need to be taken to ensure the installation accuracy of the track. It is necessary to select suitable track materials and pre-process them according to the design requirements, such as correction and polishing. Use special track installation tools to place the track on the embedded parts according to the design position, and fix them with bolts and other connectors. Ensure that the straightness, horizontality and verticality of the track meet the design requirements. In order to ensure the stability and safety of the track, pre-tightening and adjustment are also required. By adjusting the tightness of the bolts, the track will not be deformed or loosened too much during operation.
Main structure assembly and fixation
The assembly of the main structure is one of the key links in the installation of the electric single-beam crane. During the assembly process, it is necessary to follow the design requirements to ensure that the connection between the components is tight and stable. Especially for high-strength bolts and connectors, special tools need to be used to tighten them, and they must be operated strictly in accordance with the torque requirements. After the main structure is assembled, it needs to be fixed. The main structure is connected to the foundation embedded parts or other fixings by welding, bolting, etc. to ensure that it will not shake or move during use.
Electrical system installation and debugging
The installation of the electrical system is one of the important links in the installation of electric single-beam cranes. During the installation process, it is necessary to select suitable electrical components and wire and connect them according to the design requirements. At the same time, debugging work is also required to ensure the stability and reliability of the electrical system. The debugging work includes wiring of the control circuit, motor trial operation, protection device verification, etc. Through debugging, problems in the electrical system can be discovered and solved, and the performance and service life of the system can be improved. After the debugging is completed, an overall joint debugging test is also required to ensure the coordination between the various parts and the stability of the overall performance.
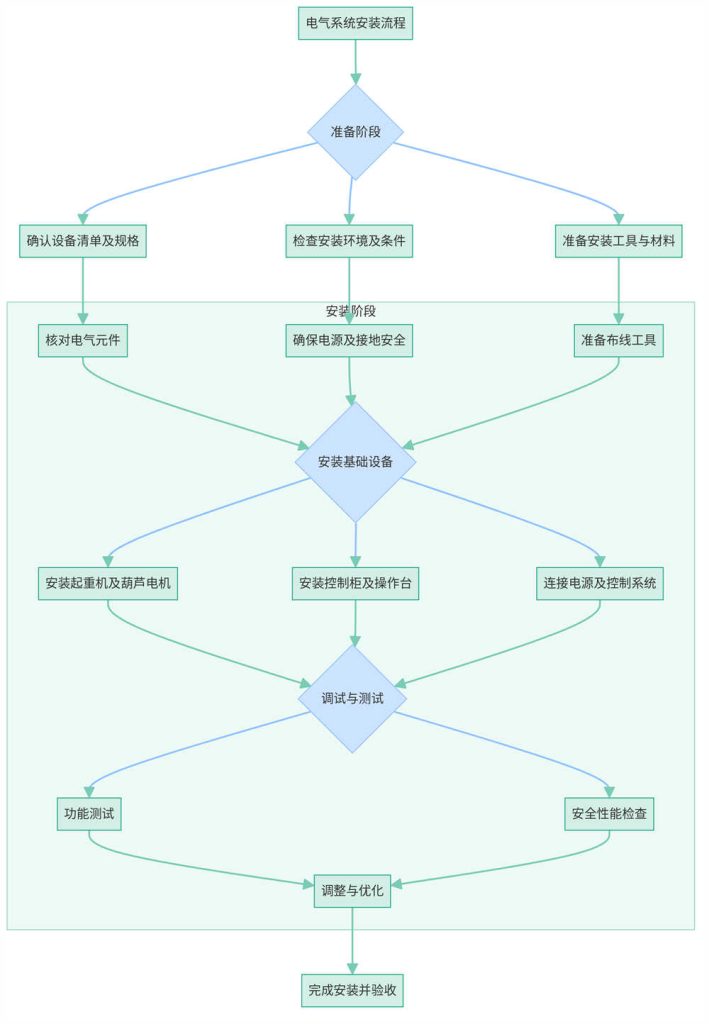
Electric hoist installation steps
Hoist body installation and fixing
First, make sure that the installation environment of the electric hoist meets the design requirements, including flat ground, no debris, no water accumulation, etc. Use special lifting tools, such as cranes or hoists, to lift the hoist body to the designated location. During the lifting process, pay attention to protecting the hoist body to avoid collisions and scratches. Connect the hoist body to the main structure of the crane and fix it with bolts and fasteners. Ensure that the connection is tight and firm to prevent loosening or falling off during use. During the installation process, the pulleys, wire ropes and other components of the hoist should also be checked to ensure that they are intact. If the components are found to be damaged or severely worn, they should be replaced in time to ensure safe use.
Hoist electrical connection and debugging
The electrical connection of the hoist needs to be carried out according to the electrical system diagram to ensure that the connection between the electrical components is correct and reliable. During the connection process, special electrical wiring tools and materials should be used, and the operation should be carried out in strict accordance with the electrical safety specifications. Before connecting, it should also be ensured that the power supply has been cut off to prevent safety accidents such as electric shock. After the connection is completed, the hoist needs to be debugged. First, check the lifting function of the hoist to ensure that it can rise and fall normally. Secondly, check the running function of the hoist to ensure that it can run smoothly on the track. Finally, check the braking function of the hoist to ensure that it can stop quickly in an emergency. Through debugging, the electrical system of the hoist can be ensured to be stable and reliable.
Installation and verification of safety protection devices
The safety protection device is an important part of the electric hoist, and its installation and verification need to be carried out strictly in accordance with the design requirements. During the installation process, it should be ensured that the position of each protection device is correct and the function is intact. At the same time, the protection device needs to be verified. For example, limit switches, overload protection devices, emergency stop buttons, etc. These protection devices can play a role quickly and accurately in an emergency, thereby ensuring the safety of personnel and the integrity of equipment. By verifying these protection devices, existing problems can be discovered and handled in time to ensure that they can play an effective role in an emergency.
Installation quality inspection and acceptance
Appearance inspection and functional testing
After the installation work is successfully completed, it is an indispensable and important step to conduct a comprehensive appearance inspection and functional testing of the electric single-beam crane and electric hoist. The appearance inspection is to ensure that the connection of each component of the equipment is firm and reliable without looseness. In particular, each connecting component such as bolts, nuts and other fasteners must be tightened strictly in accordance with the manufacturer’s requirements to avoid unstable operation or safety hazards caused by looseness. At the same time, carefully check whether the paint coating on the surface of the equipment is intact and there are no scratches or rust, so as to determine whether the equipment has been accidentally damaged during transportation and installation, and confirm that its surface protection treatment meets the design requirements and national standards.
Functional testing is to verify whether the actual operation effect and performance indicators of electric single-beam cranes and electric hoists meet expectations. This includes the test of the lifting function, that is, to test the equipment with no load and full load, check whether the lifting action is smooth and accurate, and whether the limit switch is effective; the test of the running function requires the crane to run back and forth on the track to observe whether it is stable and whether there is any deviation; the test of the braking function is also crucial, and it is necessary to repeatedly operate the lifting and running mechanism to verify whether it can stop accurately within the specified distance, and whether it can brake quickly and effectively in an emergency.
Through rigorous appearance inspection and functional testing, not only can potential problems be discovered and solved in a timely manner, but also the electric single-beam crane and electric hoist can be ensured to have a good user experience and high work efficiency during use, and meet the hoisting needs of the production site to the greatest extent.
Safety and reliability evaluation
On the basis of a comprehensive inspection of the appearance and a detailed test of each function, an in-depth safety and reliability evaluation of the electric single-beam crane and electric hoist is also required. This stage involves the detection of the load-bearing capacity of the equipment to ensure that it can still maintain sufficient load-bearing capacity under long-term and high-intensity use to avoid safety hazards caused by overload; the verification of the stability of the equipment, including but not limited to the stability during operation and the anti-overturning ability under specific working conditions, to ensure stable operation under various working conditions; in-depth analysis of the durability of the equipment, and the fatigue resistance and life of wearing parts under long-term use, so as to determine whether the equipment can maintain high reliability and low failure rate in continuous use.
Through this series of rigorous safety and reliability assessments, it can be ensured that the electric single-beam crane and electric hoist can withstand various tests during use, provide efficient, safe and stable lifting services, and meet the lifting needs of the production site to the greatest extent.
Acceptance report preparation and signing
After completing all installation quality inspections, functional tests, and safety and reliability assessments, the next step is to prepare a detailed and professional acceptance report. The acceptance report should record in detail the installation process of the equipment, the inspection results of each component, the effect of the functional test, the conclusion of the safety and reliability assessment, etc., and strive to provide comprehensive and accurate information.
After the acceptance report is completed, relevant units or experts must be invited to conduct a strict review and signature confirmation. These experts or units may include but are not limited to: technicians from equipment suppliers, professionals from third-party testing agencies, and equipment management personnel from the user. Through the joint participation of multiple parties in the review and signing of the acceptance report, it can be ensured that the installation quality of the equipment is formally recognized, providing strong guarantees for subsequent production and use. At the same time, the acceptance report will also become an important part of the equipment archive, providing an important reference for subsequent equipment maintenance and management.
Installation Quality Acceptance Form (Appearance Inspection)
Inspection items | Inspection content | Inspection results (pass/fail) | Note |
Connecting parts | Whether the bolts, nuts and other fasteners are firm and reliable, no loosening phenomenon | _ | |
Paint coating | Whether the paint coating on the surface of the equipment is complete and undamaged, without scratch marks or rust phenomenon | _ | |
Lifting function | No-load and full-load test hoisting, whether the lifting action is stable and accurate, and whether the limit switch is effective | _ | |
Operating function | The crane is running back and forth on the track, whether it is walking smoothly, and whether there is any offset phenomenon. | _ | |
Braking function | Repeatedly operate the lifting and running mechanism, whether it can stop accurately within the specified distance, and whether the emergency brake is effective. | _ |
Installation Quality Acceptance Form (Safety and Reliability Assessment)
Evaluation projects | Evaluation content | Evaluation results (pass/fail) | Note |
Load-bearing capacity | Is the bearing capacity of the equipment sufficient for long-term high-intensity use? | _ | |
Stability | Stability during operation and anti-overturning ability under specific operating conditions | _ | |
Durability | Anti-fatigue performance under long-term use, life of wearing parts, etc. | _ | |
Acceptance Report | Record the equipment installation process, inspection results, functional test results, safety and reliability assessment conclusions | _ | See attachment for details |