Workshop Cranes for Energy & Mining: Heavy-Duty Solutions for Demanding Environments
Introduction
In the energy and mining sectors, workshop cranes are essential for handling massive loads, maintaining critical equipment, and ensuring operational safety in some of the world’s harshest environments. Whether lifting turbine components, mining drills, or oil rig modules, the right crane system boosts productivity, minimizes downtime, and protects workers from high-risk manual lifts.
This guide covers:
✅ Best crane types for energy & mining applications
✅ Key features for extreme environments
✅ Safety and compliance considerations
✅ Cost factors and ROI analysis
Why Energy & Mining Operations Need Specialized Cranes
Manual lifting in these industries leads to:
✖ Dangerous working conditions (high-risk drops, crush hazards)
✖ Costly downtime (slow equipment servicing)
✖ Premature wear (improper handling of heavy machinery)
The right crane system solves these challenges by:
✔ Enabling safe heavy lifts (up to 500+ tons for wind turbines)
✔ Accelerating maintenance (3x faster than manual rigging)
✔ Reducing equipment damage (precision load control)
✔ Meeting strict safety regulations (OSHA, MSHA, ATEX compliance)
Best Workshop Cranes for Energy & Mining
1. Gantry Cranes – For Heavy Modular Lifts
Best for: Oil & gas yards, turbine assembly, mining equipment
Capacity: 20–500+ tons
Key Features:
- Outdoor-rated (corrosion-resistant coatings, IP66 components)
- Track-mounted or rubber-tired for mobility
- Custom spans (up to 40m for large components)
Ideal Uses:
- Wind turbine blade handling
- Mining truck engine swaps
- Pressure vessel installation
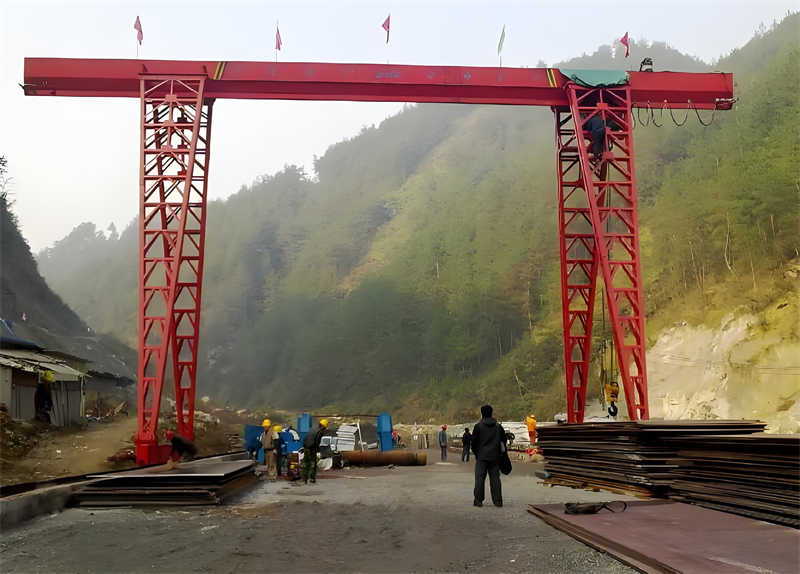
2. Explosion-Proof Cranes – For Hazardous Zones
Best for: Refineries, gas plants, coal processing
Compliance: ATEX, IECEx, NEC 500/505
Key Features:
- Spark-free motors & controls
- Stainless steel/painted construction
- Intrinsically safe pendant controls
Ideal Uses:
- Lifting in Class I Div 1/2 areas
- Coal bunker maintenance
- Chemical plant equipment servicing
3. Low-Headroom Cranes – For Underground Mining
Best for: Shafts, tunnels, confined processing plants
Key Features:
- Compact profiles (as low as 6″ clearance)
- Explosion-proof options
- Modular designs for easy underground assembly
Ideal Uses:
- Conveyor system repairs
- Loader bucket maintenance
- Ventilation equipment handling
4. Monorail Systems – For Repetitive Process Lifts
Best for: Power plant maintenance, mineral processing lines
Capacity: 1–20 tons
Key Features:
- Fixed-path efficiency
- High-temperature chains (for boiler rooms)
- Automation-ready for smelter applications
Ideal Uses:
- Boiler tube replacements
- Crusher liner changes
- Slurry pump servicing
Key Selection Criteria for Energy & Mining Cranes
When specifying a crane, prioritize:
🔹 Durability
- Galvanized/Fiberglass components for salt/corrosion resistance
- -40°C to +60°C operational range
🔹 Safety Compliance
- Overload sensors (10% above rated capacity)
- Fail-safe brakes (dual redundant systems)
- Emergency stop (ISO 13850 compliant)
🔹 Mobility & Access
- Modular designs for remote site assembly
- Radio remote controls for obstructed areas
🔹 Maintenance Features
- Lubrication-free bearings
- Modular power units for quick swaps
Case Study: How [Mining Co. X] Cut Downtime by 45%
A copper mine implemented explosion-proof gantry cranes with:
- 50-ton capacity for crusher maintenance
- IP67-rated components for dust/wet conditions
- RFID tool tracking
Results:
✔ 45% faster liner changes
✔ Zero ignition incidents in 3 years
✔ ROI in 14 months
Cost Considerations & Budgeting
Crane Type | Price Range | Key Cost Drivers |
---|---|---|
Standard Gantry | $50K–$300K | Capacity, span, outdoor upgrades |
Explosion-Proof | $120K–$600K+ | ATEX certification, stainless parts |
Underground | $75K–$250K | Low-profile design, modularity |
Monorail Systems | $20K–$150K | Length, automation integration |
Hidden Costs to Plan For:
- Foundation work (may require pilings for soft ground)
- Cold-weather packages (heated hydraulics for Arctic sites)
- Training (certification for hazardous area operation)
Final Recommendations
- Best for Heavy Outdoor Lifts: Modular gantry cranes
- Best for Hazardous Areas: Explosion-proof bridge cranes
- Best for Tight Spaces: Low-headroom jib cranes
Need Help Specifying?
➡ Our energy crane specialists offer free site assessments and ROI projections.